

You can start to monitor jobs as they’re processed from one machine to the next and monitor how each machine affects the projected completion date in real-time. For example, a part may have an effective due date and delivery date, but there are other estimated due dates in between as it’s processed. “Due dates are really the big thing with the MES. “It enables companies to make use of different programs and orders coming in that might be from the same material type for a better utilization of the cell,” says Frank Arteaga, head of product marketing, Bystronic.Ĭlick image to enlargeThe recently developed Bystronic MES solution works similarly and features Bysoft 7 as an embedded engine, but takes the visibility and control of shop floor processes a bit further, according to Arteaga. Bystronic’s Bysoft 7 Plant Manager allows users to organize laser cutting and bending programs and define which programs and materials are sent to certain machines.
Bysoft 7 nesting tutorial software#
Using the information supplied by the ERP/MRP system, nesting software can organize what programs are fed to the shop floor based on part numbers, quantities, material type, thickness variations and due dates. There’s no longer human intervention between what the ERP produces and what actually ends up at the machine.” “So you’re going straight from the ERP to production, and you’ve taken a lot of the fact checking and areas that are prone to error, and eliminating all of that in one fell swoop with a fully automated process. Nesting programs are automatically separated by machine and material type,” says St.
Bysoft 7 nesting tutorial code#
“The CAM software imports the ERP production data in the form of a spreadsheet file and generates the machine code as required. “What many vendors are doing now is offering custom development with a client’s ERP system.”įrom an ERP, Paramount’s AlmaCam software can take an Excel spreadsheet containing part specification, including part type, quantity, and material thickness and type. James, managing director, Paramount Machinery Inc. “but at some point, all of that information needs to be converted and translated to a machine program on the production floor,” explains Eric St. Besides, fabricators with ERP/MRP systems often have an assortment of technologies on the shop floor.ĮRP systems plan all of the production for the day, week, etc.

While there is OEM nesting software that is strictly designed for certain machines, there are more universal, flexible options on the market.
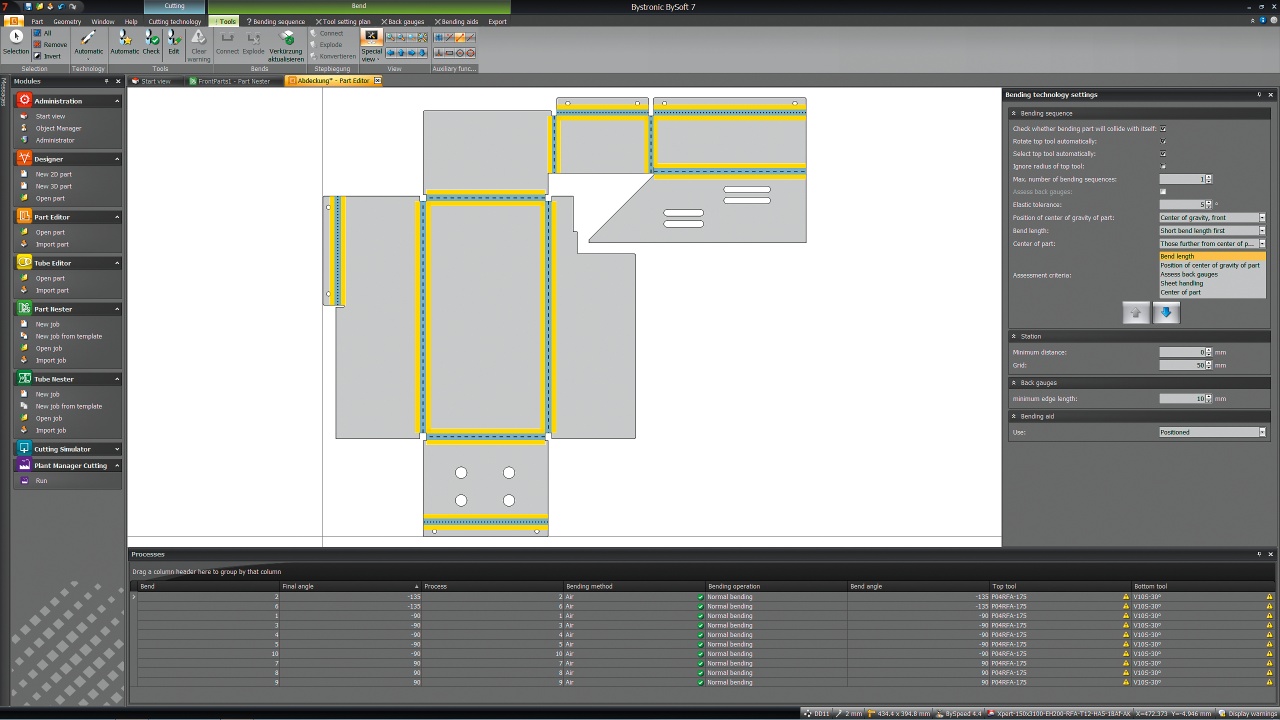
Software providers and OEMs are answering this call. “And a software that’s flexible as far as editing.”
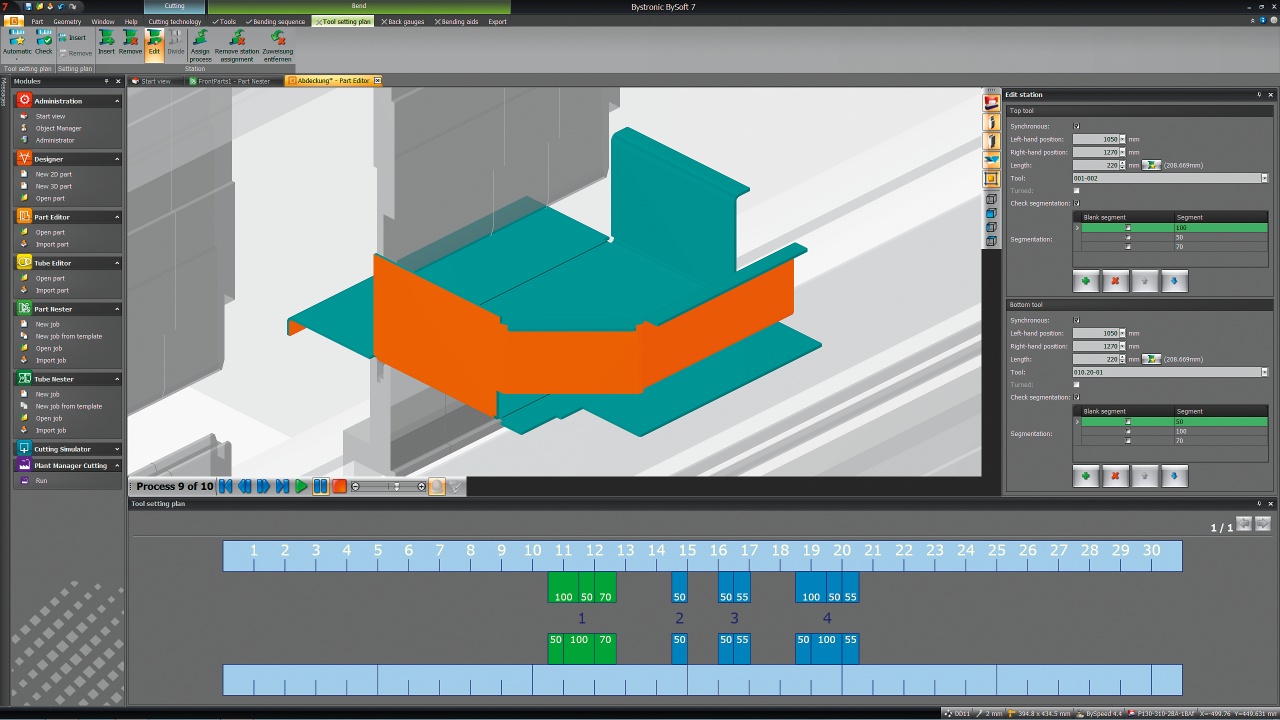
And like any software or operating system, CAD/CAM packages with nesting programs are constantly evolving with updates, tweaks, patches and new versions–all driven by customer needs and feedback–which consequently boosts not only production, labour efficiencies and material utilization, but also reduces cost.īut what is top of mind for many fabricators is to have a fully integrated system that connects programming software to their ERP/MRP systems, and it needs to be flexible and user-friendly.Ĭlick image to enlarge“The biggest request we see is for ERP/MRP integration,” says John Parenzan, Amada’s software group product manager. Of course, software plays a vital role in programming automated processes. Manufacturers have had their sights set on automation for sometime now, but in the past few years the concept of Industry 4.0 or the Industrial Internet of Things (IIoT) have become the new reality for improving efficiencies and controlling process flow.įor metal fabricators, who are too often squeezed with tight due dates, streamlining the entire process–from front-office to shop floor production–having a detailed view and control of production are all essential to remaining competitive. How nesting software is keeping pace with industry needs Click image to enlargeby Noelle Stapinsky
